As of today, we think that modern-day plastic polymers are made in the laboratory. But in reality, there are natural materials found thousands of years ago. There are Mesoamericans who used natural rubber into balls and other objects in 1600 BC. The use of adhesives, coatings, and fillers can be found in the Old Testament of the Bible.
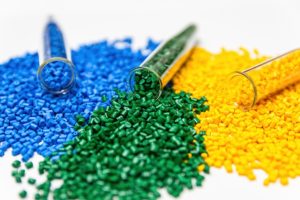
Polymers have molecules with a high number of repeating molecules called monomers and they are formed in a sequential chain. There are also naturally occurring and synthetic polymers are starches, latex, cellulose, and proteins.
These materials have long molecules that allow constructing other materials like fibers, films, adhesives, resistant paints and tough but light solids that are transformed for the modern world.
The Ebonite or hard rubber was first discovered in the early 1800s. It was the first thermosetting material. Thermosetting is a resin pre-polymer which is in a soft or viscous state that is changed into the polymer in a curing process. This curing process is completed by the action of heat or radiation under pressure which is called Thermoset.
In the year 1839, Charles Goodyear invented vulcanized rubber and Eduard Simon discovered polystyrene. Simon was a German apothecary.
Charles Goodyear joined the Roxbury India Rubber Company who is the first American rubber manufacturer in 1834. Here he was trying to sell a new valve that he devised for rubber life preservers. The company was unable to do business as there racks full of rubber goods which are melted into a big mess foul-smelling glue because of hot and dry weather. And customers returning thousands of melted rubber products. People started using the new waterproof gum from Brazil. When Goodyear came to Philadelphia was captured by Debtors in the prison where he started the rubber experiments.
When he came out of jail, continued the experiments. He made new shoes but in the summer the shoes turned into paste. He continuing the experiments and he mixed sulfur with the rubber and it is accidentally it is thrown to the hot stove. It turned into a waterproof rubber and hardened also. He had made different products with the experiments. Which are the first and most versatile of modern plastics.
In the year 1850 at the Exhibition of London, Alexander Parkes find that solid residue was left when photographic solvent evaporated. This residue was a hard, elastic and waterproof substance. After some time he patented the process of waterproofing of woven fabrics.
This same process was also discovered by Hyatt brothers and after some legal battles it is known as similar product cellulose. Today it is known as cellulose nitrate. The first-time the word plastic was used in 1925. After sometimes the German chemist comes with information that these substances are made up of 10,000 or more atom. He also studied a polymeric structure of rubber which has repeated monomers. He also receives a noble prize for his excellent work.
The research is continuing in the first half of the twentieth century. Chemists found that many natural resins and fibers were polymers. The first synthetic plastic was Bakelite which was invented by Leo Baekeland in 1907 his company producing the laminating varnish, molding material, and cast resin. The first products were motor distributor rotors, radios, and Ericsson Telephone. In the year 1940 and 1950s, the Bakelite replaced materials like cast iron and tin to make toys. The Bakelite was more durable, didn’t scratch easily and can manufacture in many colors.
In the first half of the twentieth century, the 15 new classes of polymers were synthesized. There is a range of materials developed like natural polymers, modified natural polymers, thermosetting plastics, and thermoplastics. These materials have unique properties like wide temperature usages. The materials like chemical and light-resistant. The materials are strong, tough and low cost compared to other materials.
With this beginning, today there are over 310 million tons of plastics are used annually and continue growing about 5 percent per year.
The polyethylene was developed by Reginald Gibson and Eric Fawcett in 1933. It was used as low-density resin (LDPE) by 1935. The high-density polyethylene (HDPE) was invented in 1953. There are about 25 processes are used for making other PE products. It is the second most used resin. The resin is used to make the plastic film, milk jugs, sandwich bags, cling wrap, pipes, and insulation for electric cables.
The PVC (Polyvinyl Chloride) was first commercially used in the 1920s. The PVC has a different chemical structure and has chlorine, carbon, and hydrogen. The white powder needs a blend of other products to make different products. It is used in piping, medical devices, shutters doors and upholstery, and other industrial applications.
The polystyrene was produced in the 1930s by BASF German company. The polystyrene cups are well known and their modified form is also an excellent insulator for homes and industries. It is also used in TVs and other electronic items.
The PET was discovered in 1941 and today we recognize this polyester film in many forms of bottles that are clear and resist Ultra Violet light. It is also transparent, lightweight and resistance to carbon dioxide permeation.
The polypropylene was discovered by Giulio Natta in 1954 and commercial production started in 1957. This is the most widely used plastic in the world. It is because it has low cost and versatility. It is also thermoformed, blown film blow-molded, injection-molded and extruded into and also a wide range of products like stackable crates for storage and shipping, small, thin-walled containers (yogurt, margarine tubs, food trays), glass replacement, window frames, water pipes and household goods like bowls, combs, toasters, hairdryers and film wrapping for clothing and many other applications.
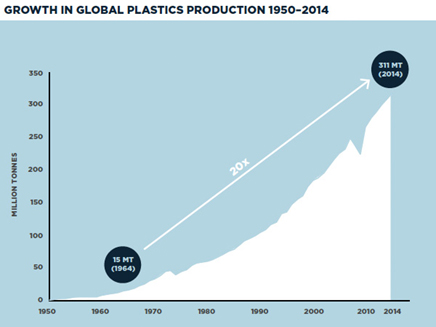
Most plastics need additives to make various products. It may be the most expensive component of the product and the range makes formulating polymers. The materials forms and additives can create a huge variety of products.
There are many benefits of plastics like lightweight, sterile and easy to manufacture. It has a strength-to-weight ratio which helpful for car manufacturers to increase the mileage. The stronger, lighter packaging bottles are very convenient and save millions of dollars in transportation.
The plastic comes at a price. The durability of the plastic makes it long-lasting. It is not easily degraded in a natural environment which is a risk for nature. The future of plastic is very bright but the industry has to find the solution for recycling.